Out of the blue: F.P. Journe and the power of independence
25 January 2024When he decided to found his own brand in 1999, François-Paul Journe had already been creating unique pieces for collectors for years. He always had a strong personal vision of watchmaking, and to this day, there is no creative team in the manufacture: he is the one who creates each watch, from design to realization. This means that he has his own view of the mechanics, i.e. the movements, but also of the dials and cases – because he creates very specific aesthetics for the brand’s watches: the same hands, the same numerals for the hour markers, the round case… The creation of his own brand basically gave substance to this unique way of envisioning watchmaking.
FRANÇOIS-PAUL JOURNE AND THE INTEGRATED MANUFACTURE
In 2000, he created Cadraniers de Genève, which in essence was a dial factory, and set up a joint venture with Max Busser, who at the time worked for Harry Winston: both wanted an independent company that would allow them to create their own dials. It is a story directly linked to the manufacture, to the independence of the brand which today produces about 95 per cent of its components in house, leaving the straps, glasses, rubies and balance springs to outside suppliers. This idea of independence has always been in François-Paul Journe’s mind, and is also very much present in today’s two companies: Cadraniers de Genève and Boîtiers de Genève.
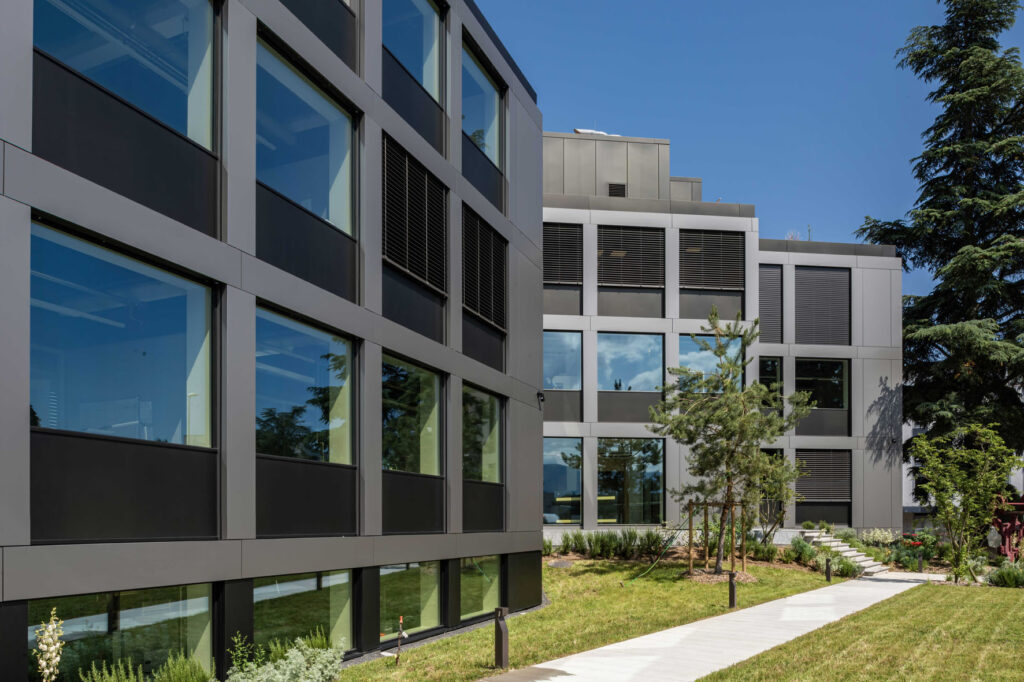
The two companies are 100% owned by F.P. Journe, and Cadraniers de Genève is a dial supplier for other haute horlogerie brands. They are directly tied to the Geneva manufacture, which creates and processes the movement components; the idea is to have a totally integrated production environment so that François-Paul Journe is entirely free to create what he wants. The prototype area plays a key role in the company, so you can immediately transfer ideas into concrete items and maintain full control over the quality of all components (without the adequate autonomy and industrial capacity, you won’t be able to produce the prototypes you need). By owning his own companies, François-Paul Journe can directly control all processes and make the necessary fine-tuning, thanks to in-house resources and machinery.
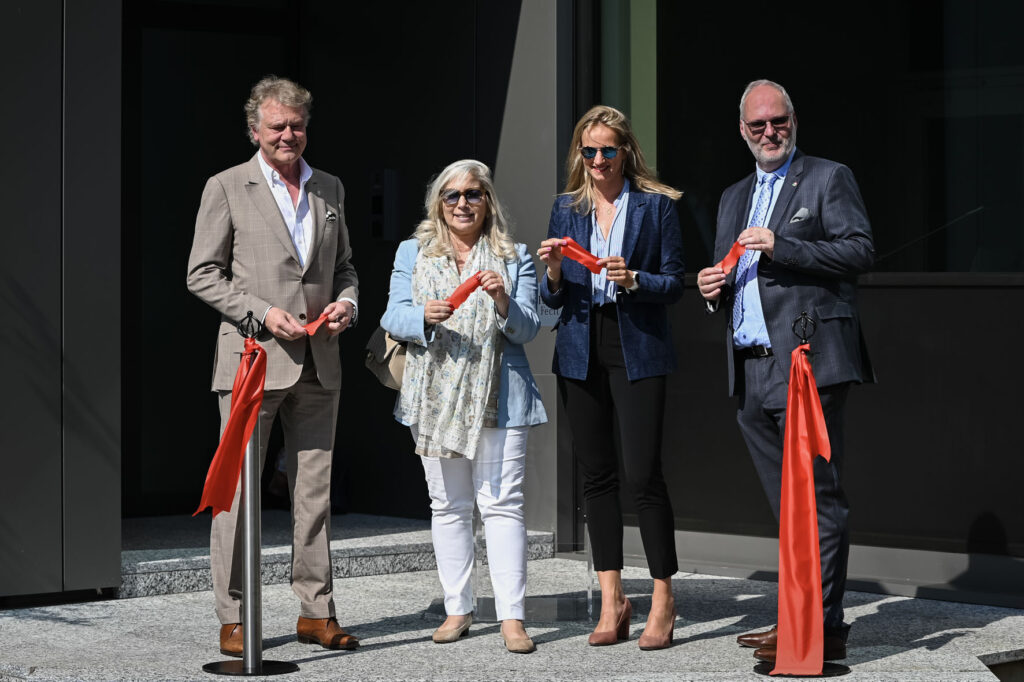
This is the idea behind the new Meyrin building where Cadraniers de Genève and Boîtiers de Genève, which had already been on the same premises since 2012, share the same space again. Inaugurated last June, the building features light-flooded workshops, designed with the aim of having precise control over environmental factors. Temperature and humidity regulation systems have been integrated to ensure optimal conditions throughout the production process, also helping to improve the working conditions of the craftsmen.
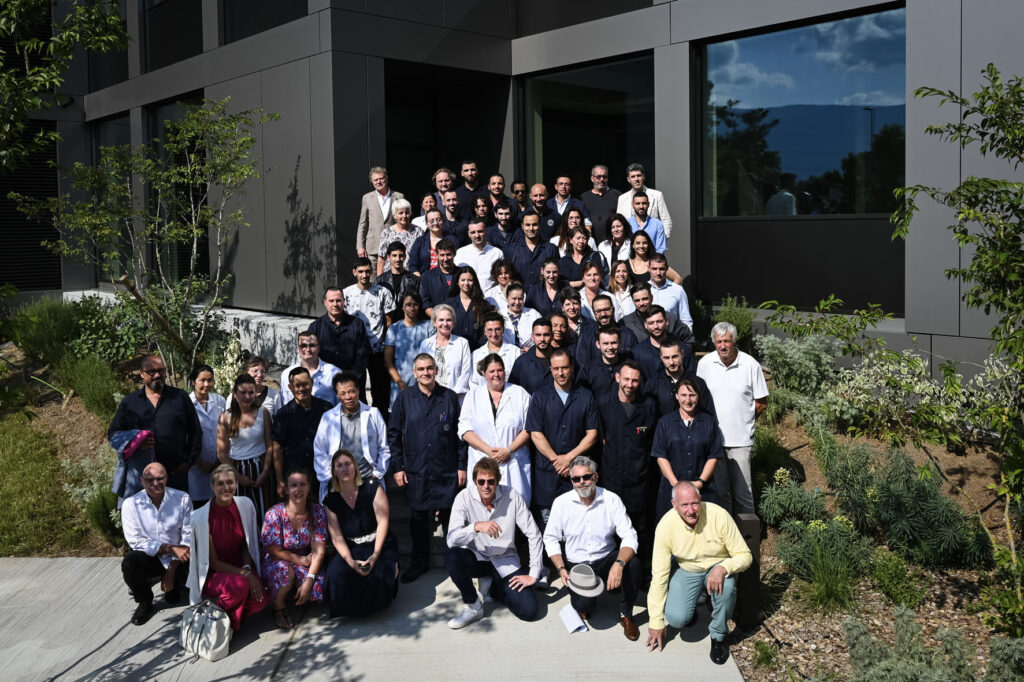
Contrary to usual expectations, the purpose of such an investment was not to encourage an increase in production but to focus on quality by developing even more efficient workshops, using modern machinery, and safeguarding the well-being of employees. About 30 people work at Cadraniers de Genève, about 40 at Boîtiers de Genève, and about 80 in the manufacture. A total of about 200 people work for F.P. Journe, including all the manufacturing and internal boutique staff.
CRAFTSMANSHIP AND INDUSTRIALISATION
At F.P. Journe, a single watchmaker works on a movement from A to Z, and is responsible for each timepiece. They have all the components and assemble them from scratch, they are responsible for both assembly and adjustment; they must ensure that the watch works perfectly and if any problem comes up during the three-year warranty period, they are responsible. The same applies to decorations: in the company there is a decoration workshop with eight people, but the watchmaker in charge also supervises the finishing. For François-Paul Journe, it is very important that a collector can, if they so wish, meet the watchmaker who supervised their watch in person.
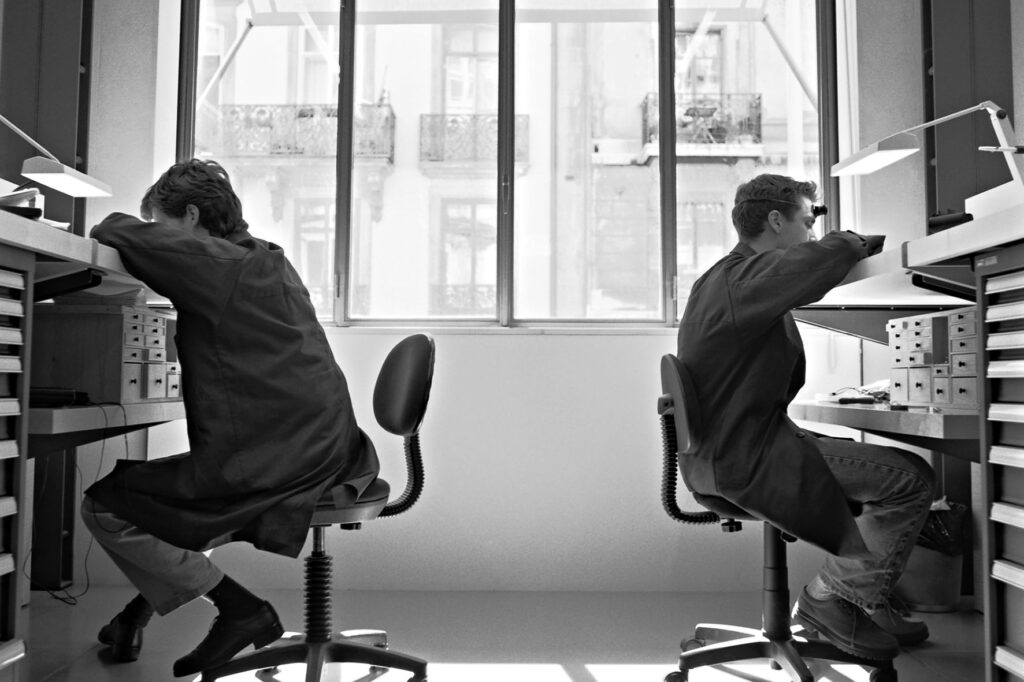
F.P. Journe produces 1000 mechanical watches a year, and between 400 and 500 electromechanical ones in the Élégante collection. Given the manufacture’s available space, the brand will not be able to increase these numbers in the future. In the Master’s idea, these are the ideal figures because it is mainly he who directs and manages everything in the company, and supervises the business processes; not exceeding a certain number of watches does not only mean not having to increase the number of employees for production, marketing, communication: as we have seen, the large investment made on Cadraniers de Genève and Boîtiers de Genève will not increase the quantity but the quality of watches, leaving François-Paul Journe creative freedom.
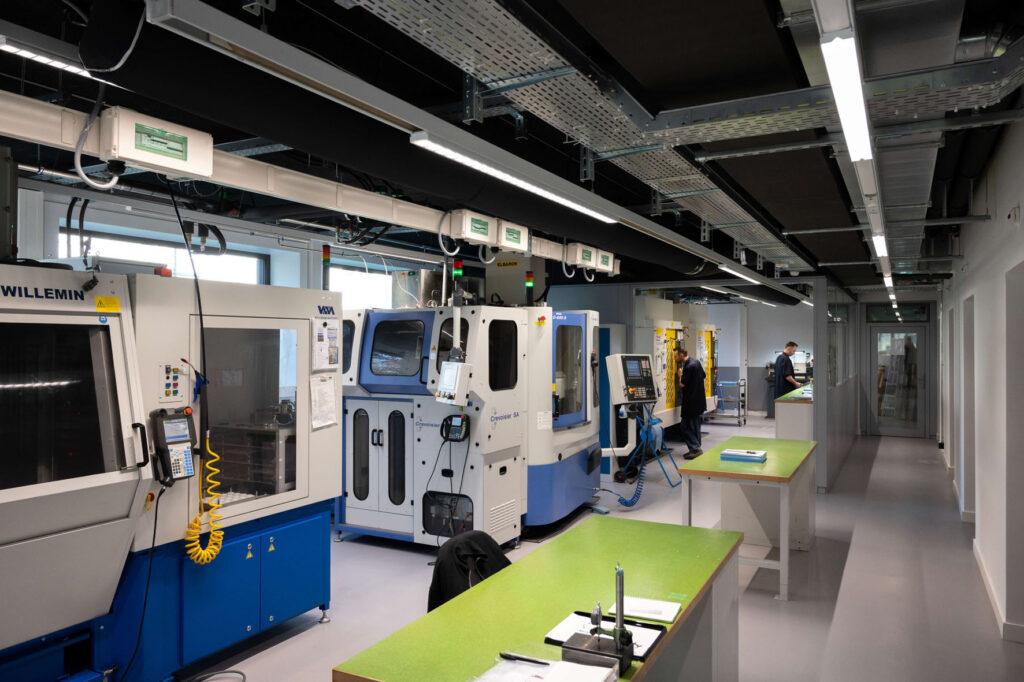
At the same time, it creates an excellent working environment, combining natural light, cozy rooms, numerically controlled machines and a large number of craftsmen, many of whom have been with the company from the very beginning and have developed high skills in applying numerals, pad printing and other techniques. At Boîtiers de Genève there was a considerable investment on new CNC machines; with the opening of the new building, for example, came an 8-axis machine that creates a case by working directly with the bar of material.
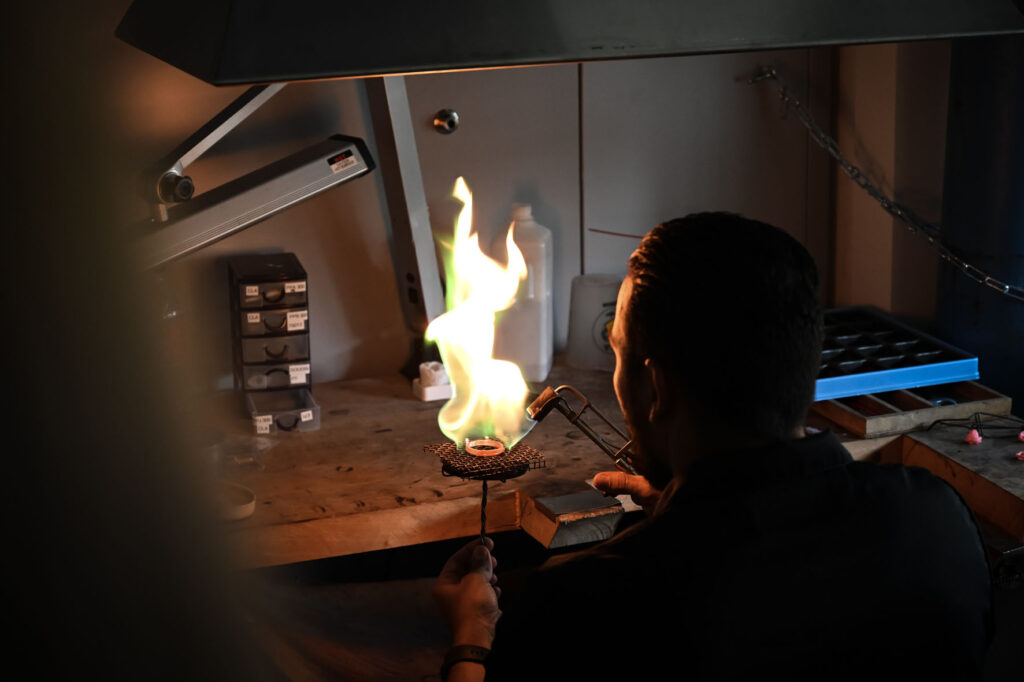
The case backs are engraved using CNC machines, and the buckles are laser-engraved using a special machine so as to ensure cutting-edge technology, but on both cases and dials the very high quality that characterises the brand cannot exist without a final human intervention. It is a perfect balance between industrialisation, technology and craftsmanship, thanks to the expertise of very experienced craftsmen.
MR SANG, THE DIAL ARTIST
Among them is Mr Dinh-Sang Ngo, a Vietnamese man who arrived in Geneva when he was 17. He has always worked with pad printing, a technique that uses a pad to finalise the creation of a dial. It requires a lot of precision, because it is the last step in the decoration after those that give the desired colour and shine to the dial: several layers of varnish must be added, at least 5 or 6, to create the classic bombée effect. For example, this technique is used to ‘print’ the indexes’ numerals on dials where these are not applied.
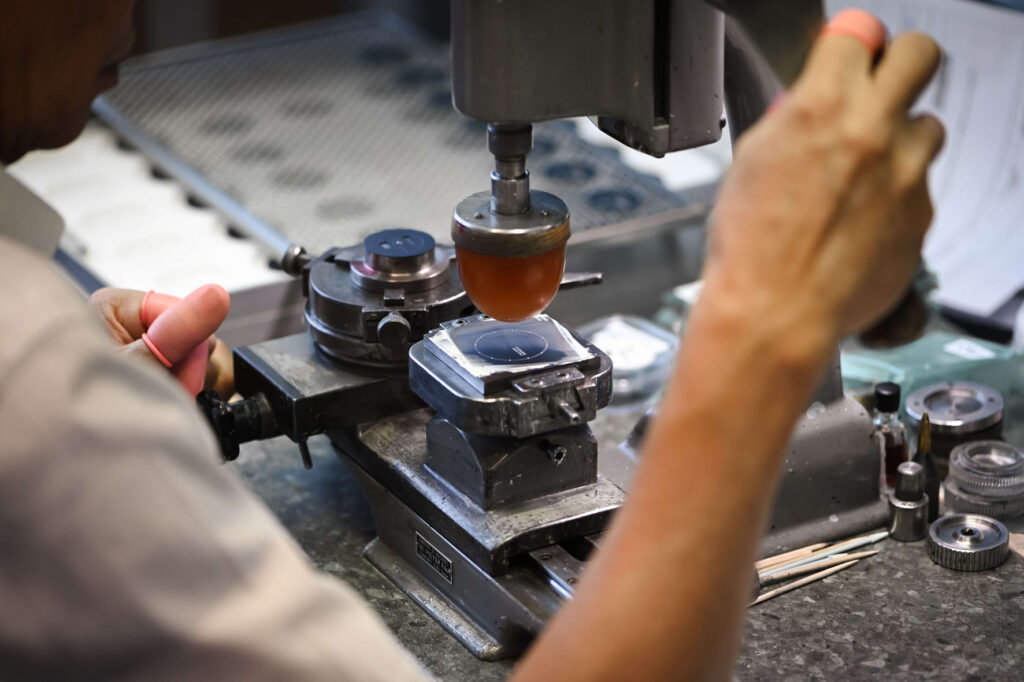
Depending on the type of dial, there are two to four pads – e.g. one for the hour markers, one for the power reserve, one for the small seconds – and four to five more layers of varnish for each of them. Each pad must be made to respect the various layers of the dial. Mr Dinh-Sang Ngo creates his own pads. While they are usually made of silicone, Dinh-Sang Ngo uses gelatine, an ancient process, a specific recipe that he has to adapt to find the perfect shape for each watch according to the dial to be printed. He is the only one to use this technique, and the only person to handle pad printing on dials in the company, but more recently he has been joined by someone he’s training for the future.
He is also the only one who can give the bombée effect to the ink on the dials. He is 65 years old and has worked as a cadranier since the beginning. He aligns the pad and dial perfectly using only his eyes, no machines or microscopes: he is like an artist and when you see him at work it seems as if he is doing the simplest thing in the world. However, he cannot remain the sole custodian of this art, it is also necessary to train the new generation and Sang is teaching the technique to one person; it will take time, because the expectation on quality is very high.
For example, a watch such as the Chronomètre Bleu has the particularity of being very thin, and many layers of paint are needed to give the dial the final deep-blue mirror look; furthermore, it is not possible to use the oven to dry the paint. On the Chronomètre Bleu, when the first print is applied, it is necessary to wait a whole night for the paint to adhere perfectly to the dial; great care must be taken and parameters such as temperature and humidity must be kept strictly under control.
THE CHRONOMÈTRE BLEU BY F.P. JOURNE
It is no coincidence that the Chronomètre Bleu is the brand’s most wanted watch: besides being beautiful, it is also particularly complex to produce. The two biggest challenges are the dial and the tantalum case. For the dial, the first step is mirror polishing. This is usually carried out only on a small part of the dial, while on the Chronomètre Bleu the entire surface is polished. Then the different layers of lacquer are added, and everything must be done by hand because each step must be extremely precise. For example, one of the most critical issues is that the dial’s base is very thin and flat, and the different processing operations can create problems.
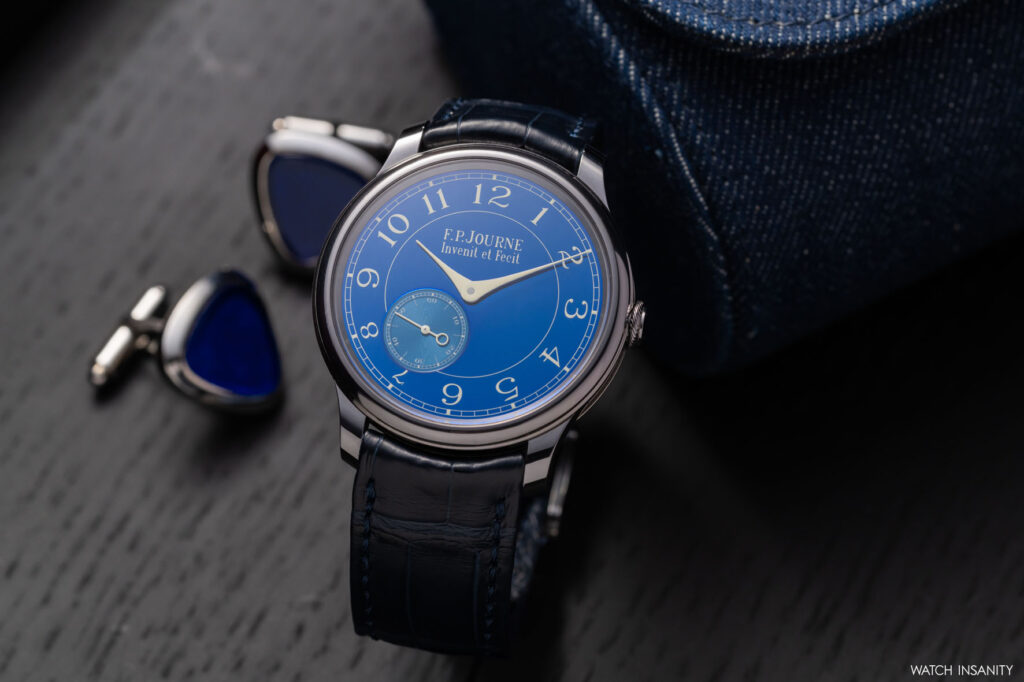
For example, during polishing, the most dangerous thing is that – as the base of the dial is very thin and obtaining a mirror polish is a long process – it might end up creating heat, which can cause the base of the dial to warp. When adding several layers of lacquer, the craftsman must be careful that each one achieves the same chromatic gradient and perfect colour; and the same with pad printing at the end, where precision is everything.
When working on the dial of the Chronomètre Bleu at F.P. Journe, the percentage of perfect dials ranges from 20 to 30%. These are all reasons why this is by far the most complex dial to create among the watches in the catalogue, and why annual production is so low.
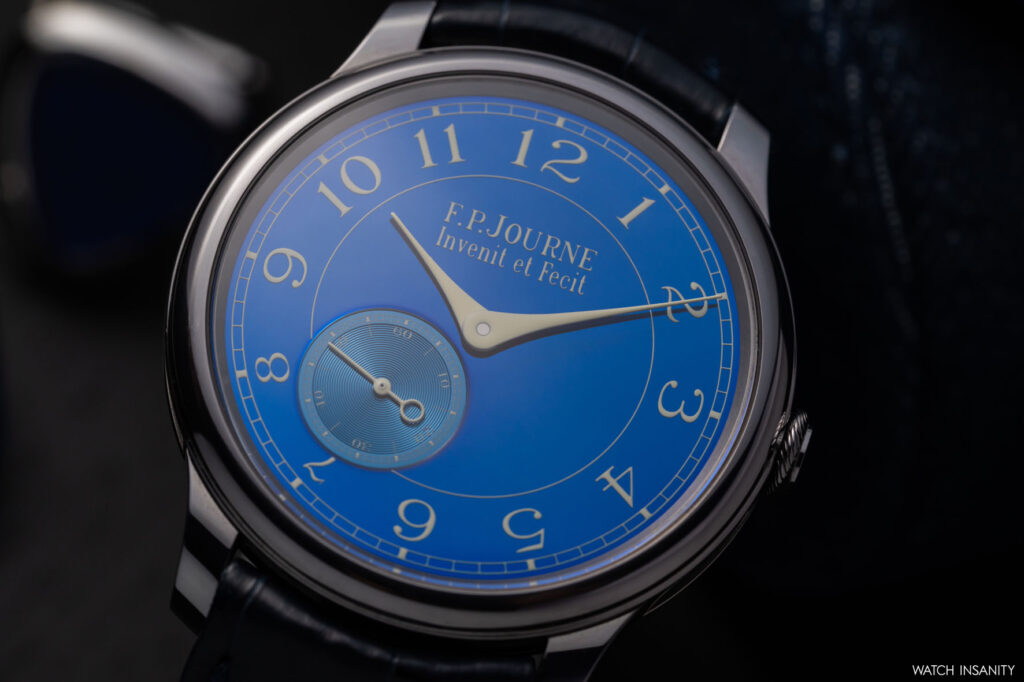
The same applies to the tantalum case, the only one produced with this metal in the collection. The challenge for tantalum lies in the workmanship. It requires the same sophisticated machinery that is used for platinum cases. While gold is very soft, for which fairly common tools used on CNC machines are sufficient because it is fairly easy to work with, platinum and tantalum require at least four times as much machinery, even diamond-tipped machines – a detail that drives up the cost. Attention must also be paid to the rotational speed of the cutters, because the tools that are used can break and damage the CNC machines. Tantalum cutters are the only ones that must be constantly supervised by a person standing close to the machine during processing.
WHY BLUE?
The Chronomètre Bleu was created in 2008 to be F.P. Journe’s most reasonably priced mechanical watch in the catalogue with a strong value proposition, and it still is, despite the fact that, as we have seen above, producing it is super challenging. It is also the only time-only timepiece without a power reserve and with a 39 mm case: this too greatly increases its value and desirability. It is something completely different from all the brand’s other watches and it represents a real challenge, not only for the cadraniers but also for the boîtiers, as not many watchmakers in the world are able to create tantalum cases.
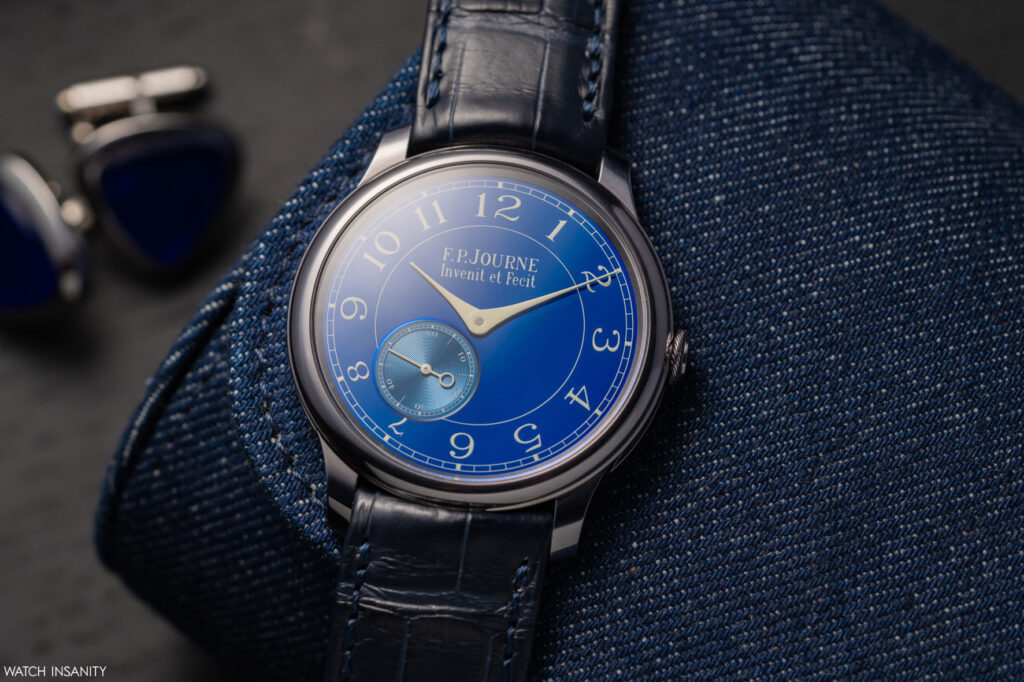
The blue of the Chronomètre Bleu is an entirely aesthetic choice; François-Paul Journe has never spoken of any particular reason why he wanted this colour. In addition, the tantalum case has a grey-blue colour that best matches the dial, which on the Chronomètre Bleu aesthetically prevails on the movement for the first time. François-Paul Journe is indeed a watchmaker but also a designer, who makes all the aesthetic decisions, including that of having a watch with this deep, mirror-like colour.
FRANÇOIS-PAUL JOURNE AND HOSPITALITY
Watchmaker, designer, but also refined host. Since 2003, with the opening of the first boutique in Tokyo, François-Paul Journe has always wanted not only a shop but a place to invite and host collectors, not designed only for sales but as an environment in which to talk, discuss, relax. A concept made even stronger in the two Maisons Journe, in Miami and New York, which are different and larger from the boutiques, with a large bar; there is also a bartender in Miami who is himself part of the team, always promoting the hospitality philosophy by offering a true experience.
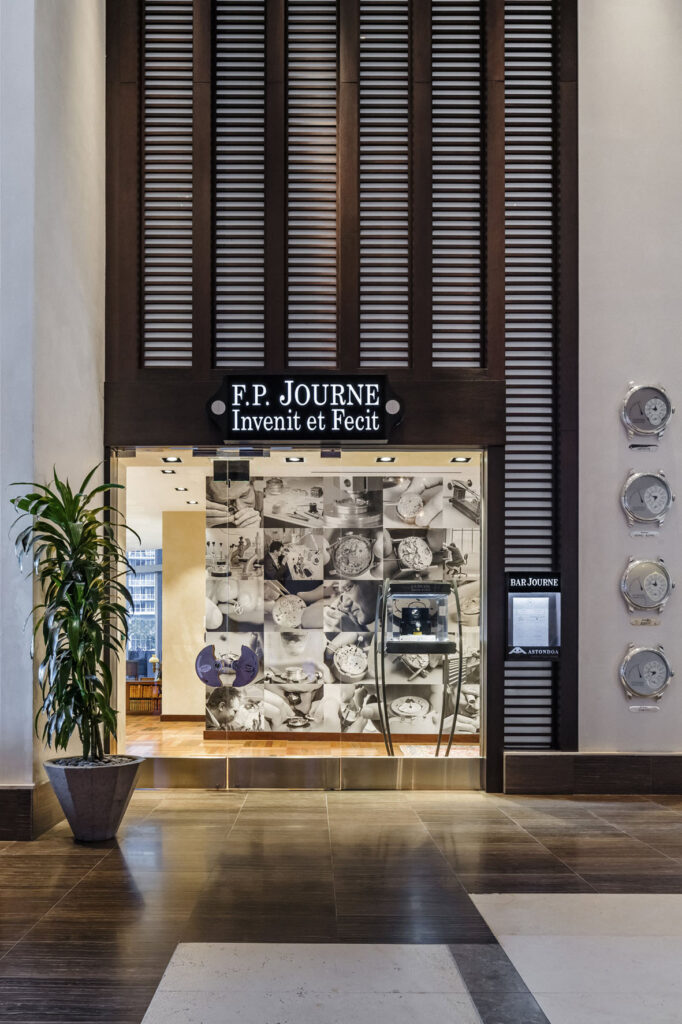
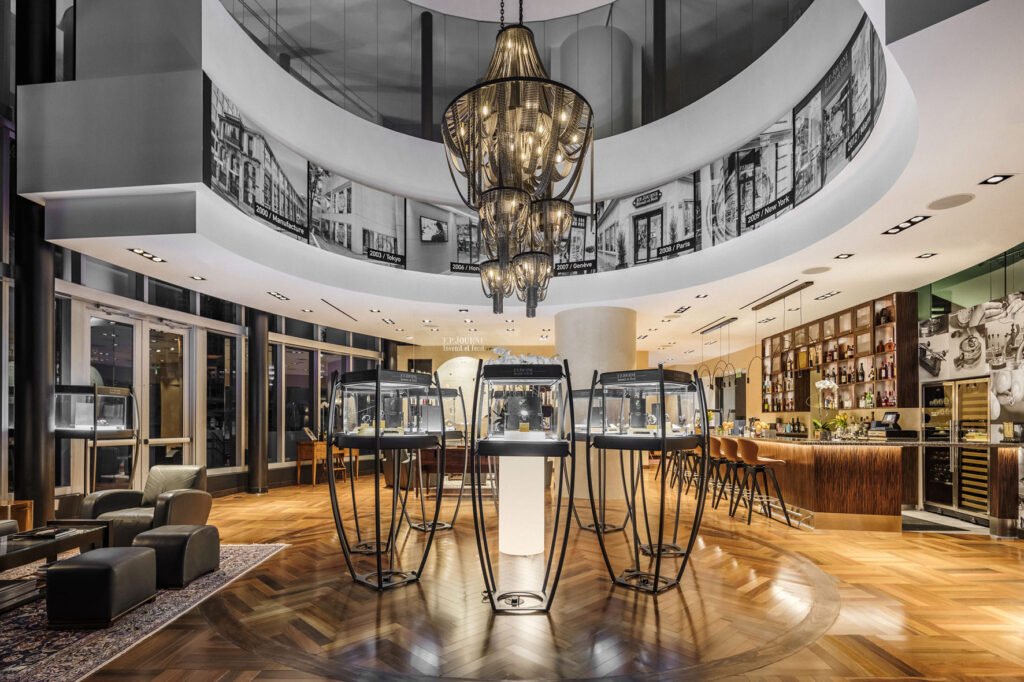
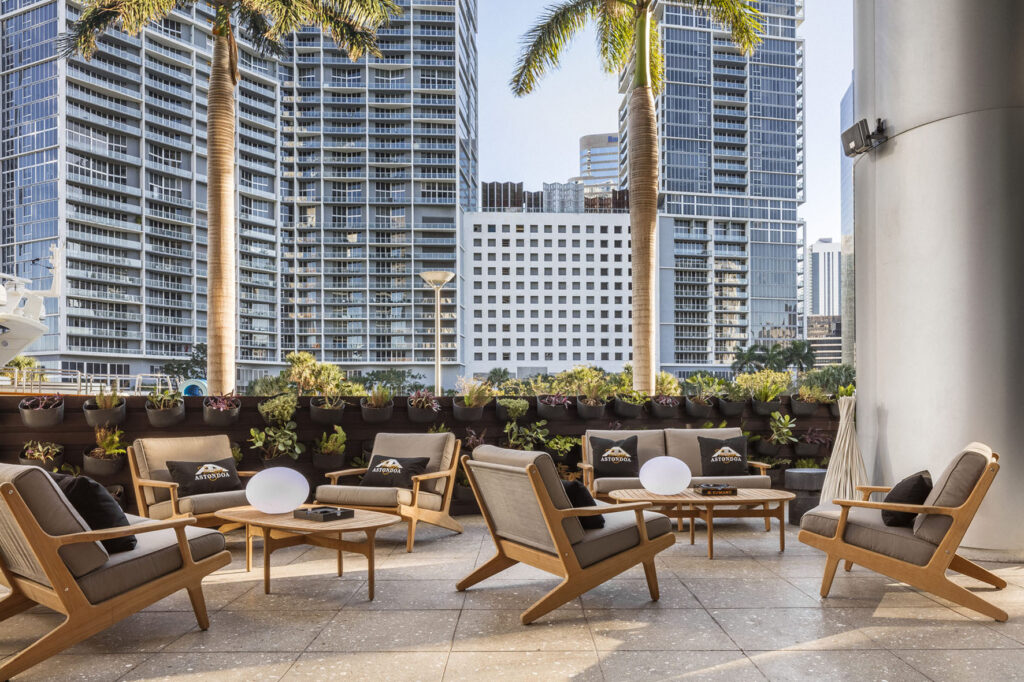
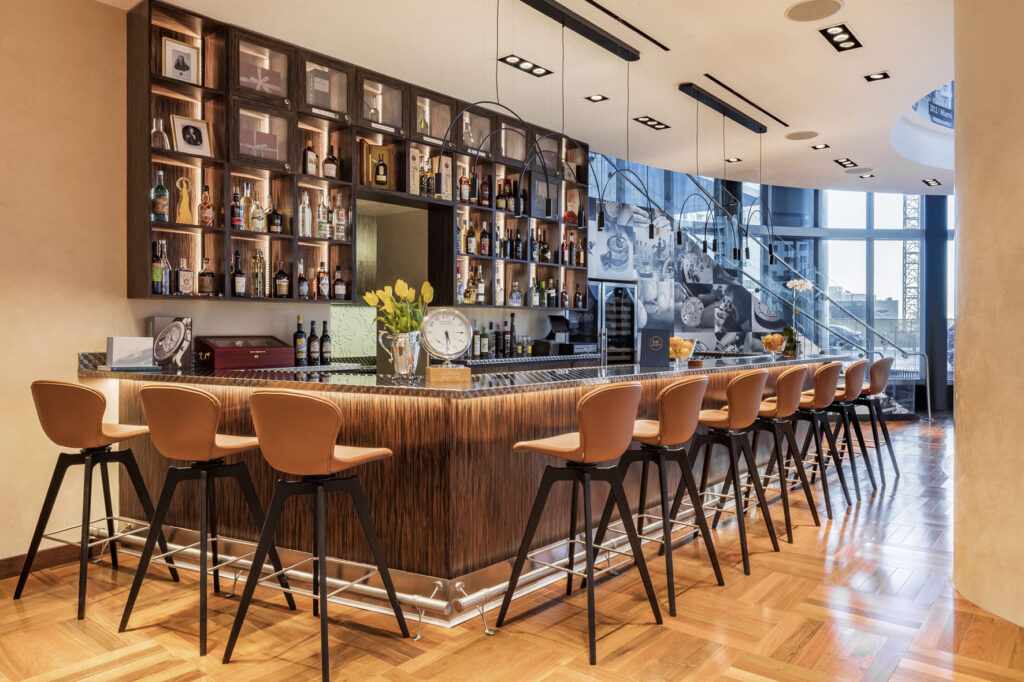
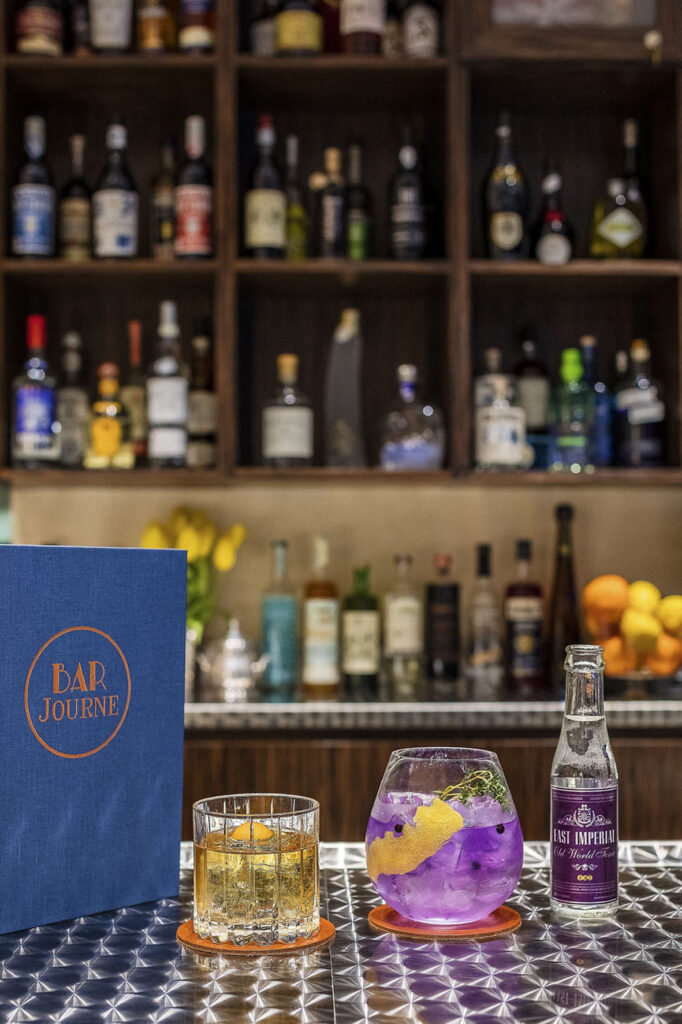
The same philosophy applies to the restaurant that has just opened in Geneva: 54 covers, a place to meet and host enthusiasts and collectors. It is the result of the work of two people who have developed two communities and strong relationships, each in their own fields. Starred chef Dominique Gauthier has a precise vision of cuisine and hospitality and decides everything about the food, François-Paul Journe decides everything about the decoration and mise en place. Each table is named after a great watchmaker of the past, the only contemporary one being François-Paul himself, who has his own table. On the walls, 11 posters with movements or technical drawings make the connection between haute cuisine and haute horlogerie. After all, François-Paul himself loves good food and good wine and is also an excellent cook: he puts precision and passion not only into watchmaking but also into cooking.
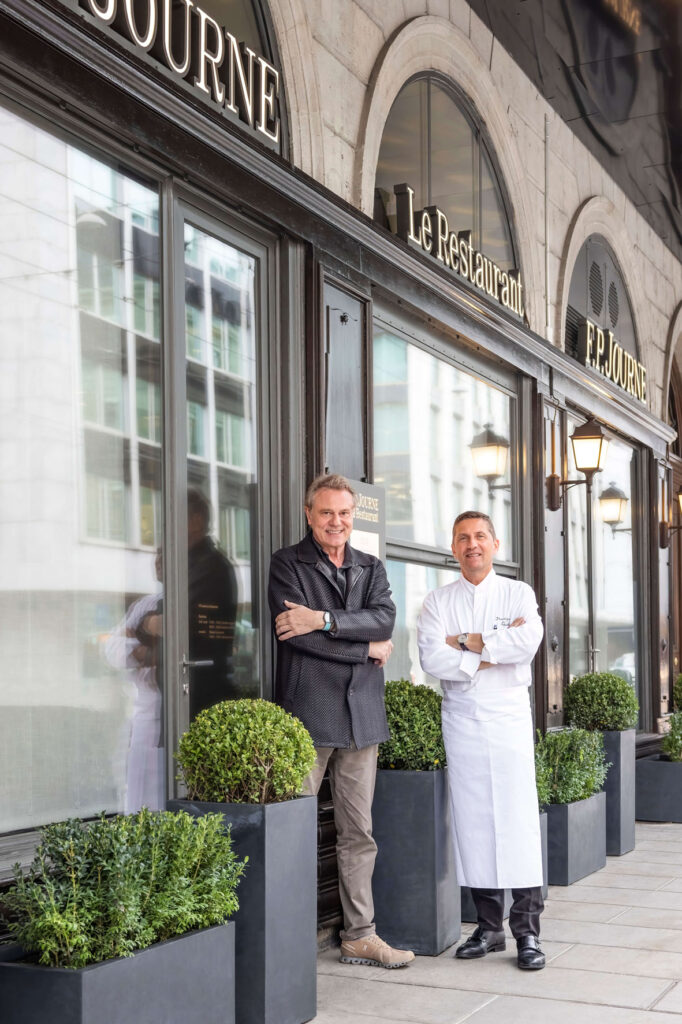
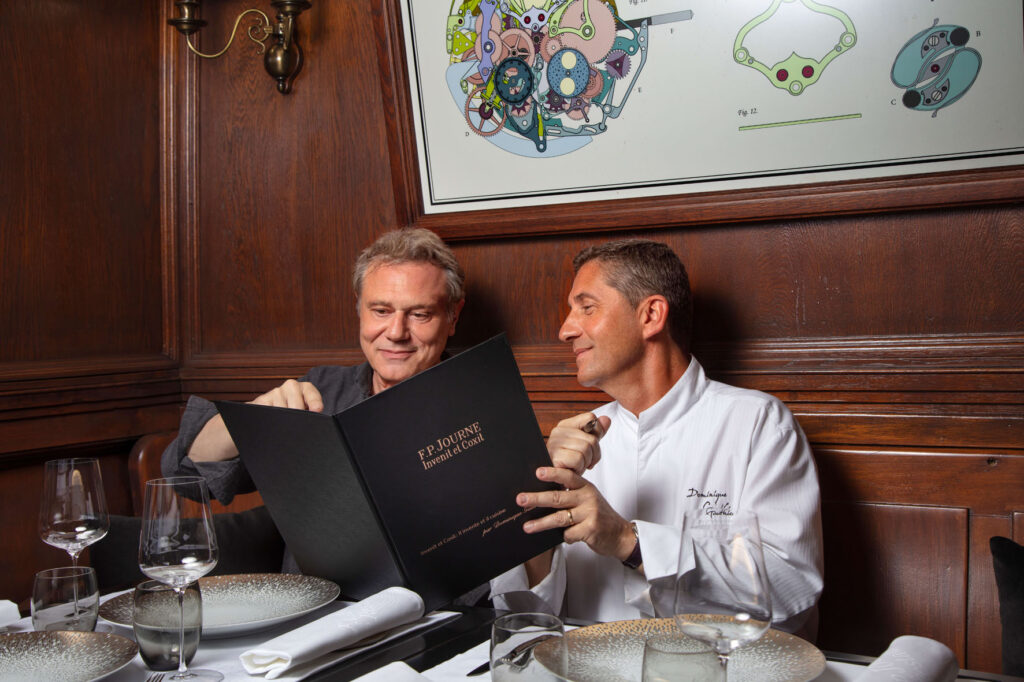
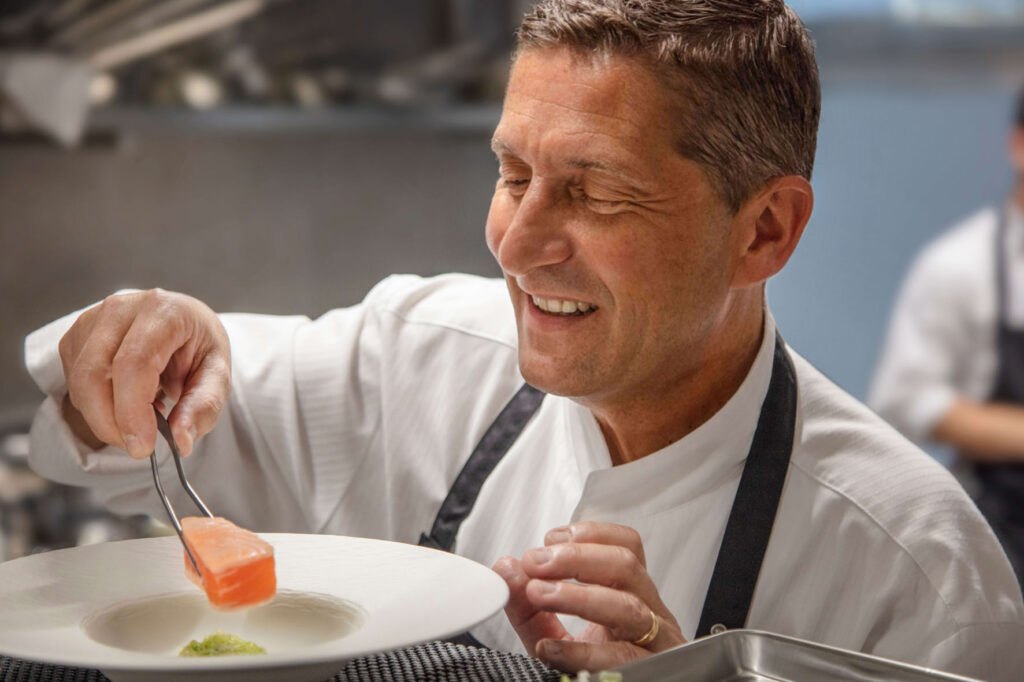
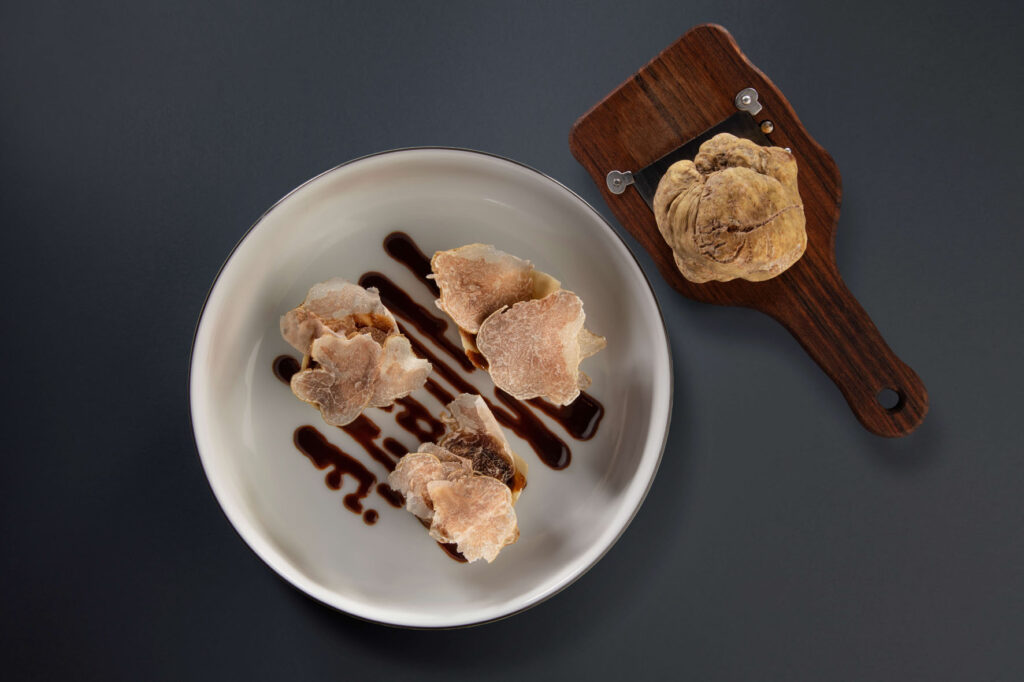
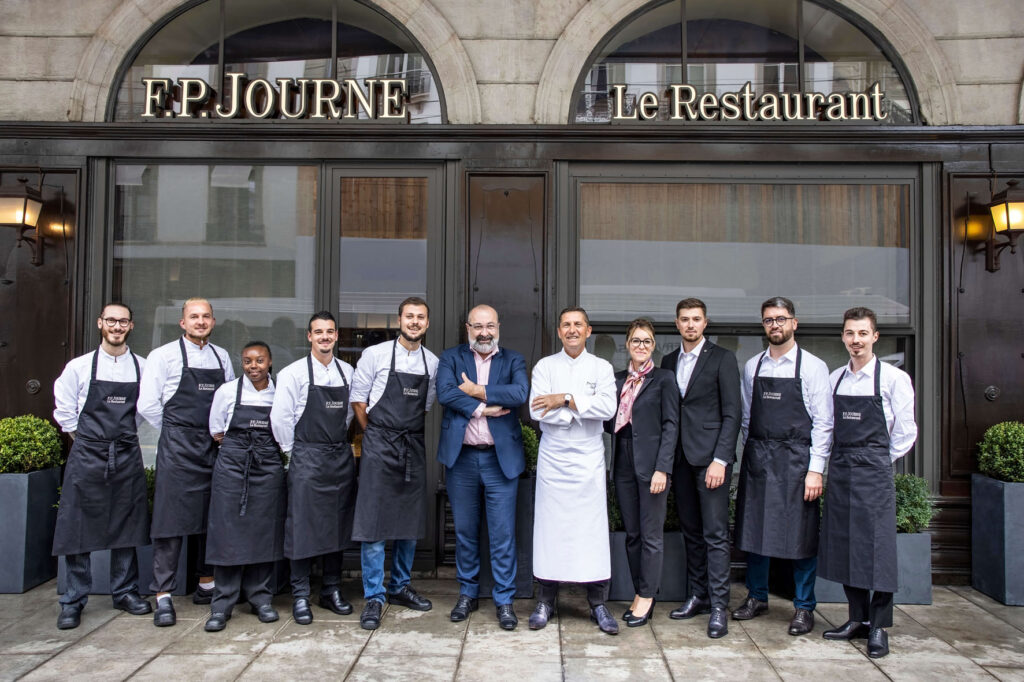
It may seem like an insignificant detail, this hospitality, but it isn’t. It is the natural completion of the personal and professional journey and production philosophy of a man who, over little more than twenty years, has been able to elevate watchmaking to an unprecedented level. Because François-Paul Journe is not just a master, F.P. Journe is not just a brand, the Chronomètre Bleu is not just a watch. They are the three faces of two concepts at the heart of haute horlogerie: artistic excellence and striving for perfection.
By Davide Passoni